In many countries, producers of electronic or electrical equipment are also responsible for offering a takeback system for consumer electronics at end-of-life. To measure the performance of these systems, manufacturers and importers are obliged to report to the local government. Measurement is often based on a percentage of the collected weight versus the weight placed on the market. Every year it seems the target is set higher, in order to increase the percentage of collected products: an important but challenging task.
However another challenging task is motivating consumers to send in their old electronics. According to Business Insider, Americans have $33.8 billion worth of unused cell phones. Often, items such as old smartphones, laptops and other electronics end up in drawers and attics, and will not be sent for recycling for many years.
Currently only 20 percent of electronics are reported as being recycled, leaving the 80 percent to have ended up in a landfill, or entering the informal recycling sector. If products are exchanged under warranty, they may be repaired or disposed of in a different country – which can make affect these types of reports, which can make it challenging for regulators and recyclers.
For the 20 percent of e-waste that is collected for recycling, new efforts are being made to reuse the plastic for new products. This has begun to create an increasing demand for recycled plastics and original equipment manufacturers (OEMs) are in need of a reliable, high-quality feedstock of recycled plastics to fulfill future production needs.
When these trends and challenges are combined, a gap is identified: The lack of recycling of valuable products, which has a negative effect on the volume of available recycled plastics. It is important to keep in mind, when electronic products are sent for recycling they should be delivered to a party that is also capable of retrieving plastics from this stream. This is essential for closing the loop on plastics and fulfilling collection rates.
Together with producers, activities are being launched to obtain more control on the return flow of products. Plastics is one of the most significant components of consumer electronic waste (e-waste), accounting for nearly 20 percent or more depending on the type of consumer products. To include plastics from e-waste in the resource-efficient circular economy, another set of challenges related to its end-of-life options need to be addressed.
Research by the PlasticsEurope Market Research Group (PEMRG) with Conversio Market and Strategy GmbH shows that global plastic production reached 348 million tonnes in 2017. China is the world’s largest producer of plastics, followed by Europe and North America. Between 2006 and 2016,
- plastic collected for recycling increased by 79 percent,
- energy recovery increased by 61 percent, and
- landfill decreased by 43 percent.
Insufficient Recycling Capacity
Across Europe, and potentially in other regions, there is insufficient capacity to process the various types of plastic from e-waste. Sims Lifecycle Services (SLS) is seeing a trend similar to what we have seen with metals, which is that processing companies will cherry-pick the most profitable and easiest-to-process materials.
As a result manufacturers are more closely examining their options in order to control their end-of-life products for material recovery (including plastics), and look for specialized partners to support them.
Complicated Materials
In order to deliver separated plastic resources ready for upgrading, the quality of targeted materials has to meet high-purity criteria. This places significant demands on plastics separation systems and thus involves significant investments.
Recycling plastics from waste electrical and electronic equipment (WEEE) is more complicated than recycling ‘regular’ plastics due to the presence of brominated flame retardants (BFRs) in the older products.
Stockholm convention guidelines state that recycling or final disposal of articles containing BFRs must be carried out in an environmentally-sound manner and that separated plastics may only contain a very low spec of BFRs as stated in international law and regulations.
Plastics containing high percentages of BFRs should not be recycled for reuse. The EU directive on WEEE management also states that plastics with BRFs should be separated from other WEEE plastics.
Plastic streams coming from electronics contain ‘target’ plastics that can be retrieved, which includes plastics such as polypropylene, polyethylene, polystyrene, acrylonitrile butadiene styrene, polymethyl methacrylate and ABS/PC (polycarbonate). The remainder is a highly complex mixed stream, containing non-accepted brominated flame retardant, which may not re-enter the market.
In today’s virgin materials the restricted flame retardants have been phased out, but older plastics often still have very high levels. The experience is that new as well as older materials can be end of life at the same time.
Creating a Circular Approach
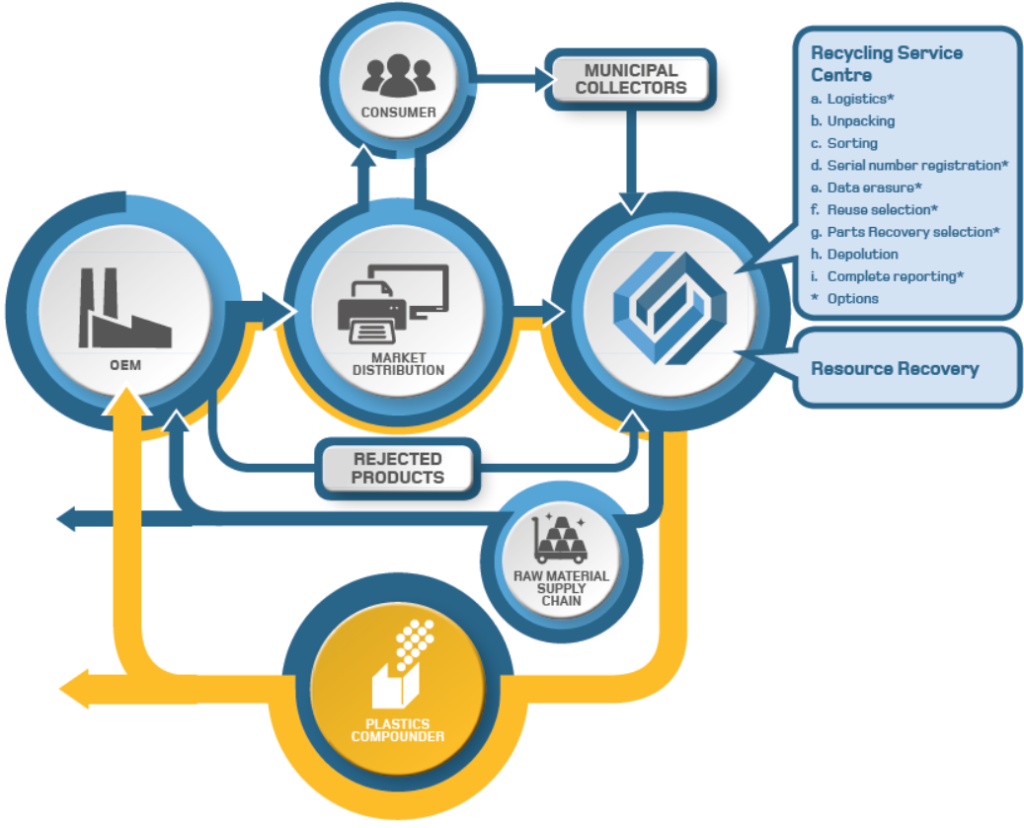
OEMs are under pressure to find a solution, especially as they consider their use of plastics over the years. Many are searching for a new approach most likely involving themselves, the separators, and the creators of the pre-concentrate.
Hewlett-Packard (HP) is a great example of a multi-national information technology company who has developed a sustainable business case. HP has created a process with SLS, to retrieve and separate recyclable plastics which are then sent back to HP to be used in new HP products.
How can this process work? HP and SLS have spent years discussing and trialing this process to ensure the solution considered all elements including the best materials recovery with operational and infrastructure costs considered.
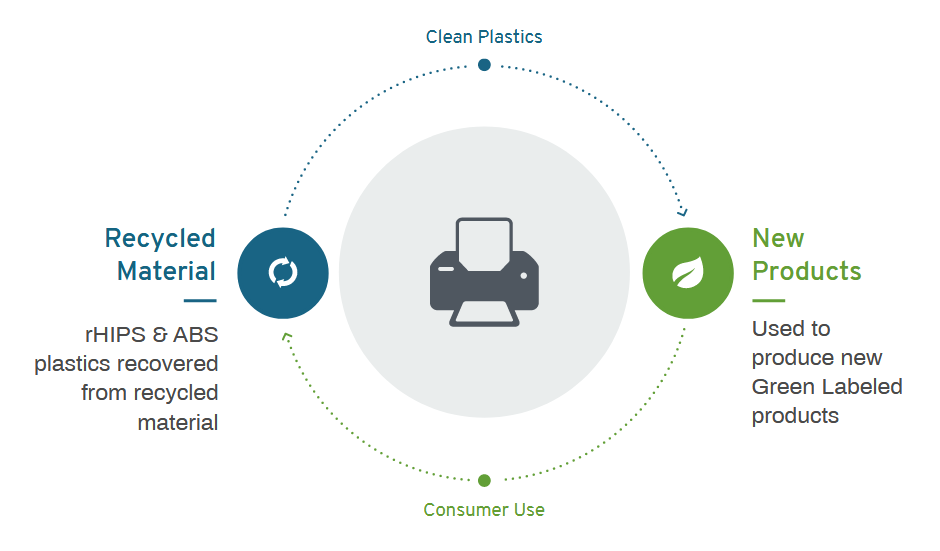
This trial resulted in clean plastics from used HP products being brought to SLS for shredding and separation. This separation creates streams of target plastics and non-target, using a combination of technologies. rHIPS and ABS plastics are then able to be recovered and used to produce new green-labeled products.
With more than 108,500,000 computers sold this year around the world, one can only assume there are more major manufacturers considering a similar circular approach.