SLS is at the forefront of developing innovative e-waste recycling solutions.
e-Recycling Programs for OEMs
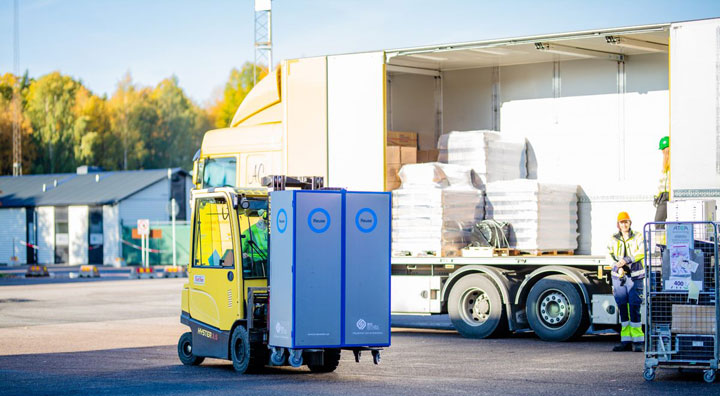
While consumer e-waste recycling is straightforward. recycling and destruction projects for electronics manufacturers are more complex. OEM recycling projects typically include service definition, service level agreements, defined security protocols and detailed reporting to meet strict corporate compliance requirements.
Some equipment requires more effort in one phase than another. For instance, closer attention is paid to equipment with batteries as these can be a fire hazard in addition to being a health hazard. Printers also contain higher percentages of plastics so plastic separation becomes an important part of responsibly recycling printers.
It is common for us to manage multiple programs for the same manufacturer, based on product type, whether we are destroying new or used equipment and if data destruction is required. Different material streams will require different reporting and tracking. How different material is sorted will be defined during the on-boarding process with SLS.
The building blocks of a more complex project may consider these factors:
Pickup Request
Using the Sims Portal, a client requests a pickup with more detailed information about the material than strictly weight. It is common to specify piece counts, weight, and type of product to be picked up.
Logistics
- Pickup and Transport – Many electronic OEM destruction projects require secure transportation to ensure all equipment is tracked and quantities confirmed. SLS offers multiple transportation providers, always finding the right balance between security and cost.
SLS Receiving and Inventory
- Deboxing/Unpacking – Most channel returns we receive are in their original retail packaging. Our sites are equipped to receive products in multiple formats such as pallets, boxes and retail packaging. Our staff will unbox the products and separate packaging materials for recycling.
- Sorting and Tracking – This step drives final inventory reporting. Sorting and tracking is most commonly by serial number, RMA number or asset classification (type, color, size, shape). We scan and report serial numbers of complete products and/or parts as needed. With this service clients have more visibility into their reverse supply chain and stock. Reporting will provide insight as to which products and parts have been recycled and destroyed.
- Inventory and Stocking – SLS can store and register your products as needed. On request we can report back to you about the status of your inventory and redeploy products as needed.
Processing
- Battery Removal – Batteries require special handling when recycling electronic equipment. SLS manually removes these hazardous items from equipment prior to recycling. Batteries are safely packaged and sent to downstream vendors for final processing.
- Data Destruction – Some products contain sensitive company or personal data which needs to be erased to ensure data safety. Data destruction methods include erasing, degaussing and shredding of storage media
- Parts Recovery – We recover spare parts for repair of in-service assets. In addition to financial return for electronic manufacturers, parts recovery contributes to the circular economy, prioritizing reuse over recycling.
- Resale – With the approval of our clients, we refurbish and resell whole units. Refurbishing equipment prior to resale increases the financial return for our clients. SLS has an excellent reputation in selling equipment in secondary markets.
- Responsible Recycling – All of our recycling programs make use of demanufacturing and resource recovery through mechanical shredding. Products are shredded, granulated and separated by commodity type into multiple secondary raw materials. All of this is achieved with the highest material yield and lowest environmental impact possible.
- Shred Size – Many electronic manufacturers will specify a small shred size for destroying proprietary equipment. This ensures all identifying characteristics of the equipment are destroyed, protecting the confidentiality for the manufacturer.
- Witnessed Destruction – Some products demand a witnessed destruction process. SLS offers the option to witness the destruction of products by clients, either in-person or via webcam.
Reporting
- Certificate of Destruction – By issuing our certificate of destruction SLS guarantees that your e-waste or other proprietary equipment is recycled and destroyed in an environmentally compliant manner. This document confirms and finalizes the audit trail and includes order number, date of destruction, weight (lbs or kg) and SLS technician confirmation. Certificates of Destruction are available via e-mail or through the Sims Portal.
- Material Fraction Report – Every shipment is weighed upon receiving at SLS. If required we can monitor the weights during our recycle processes and provide you with a detailed mass balance report. This report provides full accountability for all material received and recycled.
- Certificate of Sustainability – The Certificate of Sustainability shows the beneficial environmental offsets (carbon reduction) gained by reusing and recycling electronic equipment.
- Inventory Report – This report summarizes information based on how items are sorted and tracked. Depending on your specific program, this report will include weight or quantities, equipment type or classification, such as color, size, shape, serial number or RMA number. This report documents an audit trail and provides evidence of materials received by SLS.
- Material Invoice – The material invoice provides a financial summary of charges and credits on a monthly basis.